Top Packaging Machine Repair Solutions for Enhanced Operational Performance
The Ultimate Guide to Product Packaging Maker Fixing: Maintain Your Operations Running Smoothly
In the realm of packaging, the effectiveness of operations hinges substantially on the dependability of equipment. Recognizing the details of product packaging equipment fixing is crucial for maintaining optimal performance and minimizing disruptions. Regular upkeep not just expands the life of these makers yet likewise addresses typical problems that can hinder productivity. As we explore the nuances of troubleshooting and the critical decision-making procedure in between repair service and replacement, it becomes clear that a proactive approach can generate significant benefits. What particular strategies can companies apply to guarantee their packaging procedures continue to be undisturbed?
Value of Routine Upkeep
Routine maintenance of product packaging devices is crucial for making certain ideal efficiency and durability. By implementing an organized maintenance timetable, operators can recognize potential concerns before they rise into substantial problems. This positive approach not only minimizes downtime however additionally extends the life-span of the equipment, eventually leading to decreased functional costs.
Routine examinations permit the analysis of crucial elements such as sensors, belts, and seals. Attending to damage quickly stops unanticipated failures that could interrupt manufacturing and lead to costly repair services. In addition, regular maintenance helps guarantee conformity with sector criteria and regulations, fostering a risk-free functioning atmosphere.
In addition, upkeep tasks such as calibration, cleaning, and lubrication considerably improve maker effectiveness. Boosted efficiency converts to regular item top quality, which is crucial for keeping consumer contentment and brand name online reputation. A properly maintained product packaging equipment runs at ideal rates and minimizes material waste, adding to overall productivity.
Usual Product Packaging Equipment Problems
Packaging devices, like any complex equipment, can run into a selection of typical issues that may prevent their efficiency and effectiveness - packaging machine repair. One prevalent problem is irregular sealing, which can result in item putridity and wastage if plans are not appropriately sealed. This frequently arises from misaligned elements or worn securing aspects
Another frequent concern is mechanical jams, which can happen due to international objects, used parts, or improper placement. Jams can trigger hold-ups in production and increase downtime, inevitably affecting total efficiency. Additionally, digital malfunctions, such as failing in sensors or control systems, can interfere with operations and lead to imprecise measurements or erratic maker behavior.
Moreover, problems with item feed can additionally emerge, where items might not be delivered to the product packaging area constantly, causing disruptions. Wear and tear on belts and rollers can lead to suboptimal efficiency, requiring instant focus to prevent additional damages.
Recognizing these common problems is essential for maintaining the stability of product packaging procedures, ensuring that machinery runs efficiently and successfully, which in turn assists in meeting manufacturing targets and keeping product quality.

Troubleshooting Strategies
Reliable fixing strategies are crucial for immediately dealing with concerns that develop with packaging equipments. A methodical approach is crucial for identifying the origin of breakdowns and lessening downtime. Begin by collecting info about the signs observed; this may consist of unusual noises, functional delays, or mistake codes displayed on the equipment's interface.
Following, refer to the maker's guidebook for fixing standards particular to the version concerned. This this content source can give important understandings into typical concerns and recommended analysis actions. Utilize visual examinations to check for loosened links, worn belts, or misaligned elements, as these physical variables frequently add to functional failures.
Execute a procedure of removal by testing individual maker features. If a seal is not developing appropriately, assess the sealing mechanism and temperature settings to figure out if they fulfill functional specifications. Document each step taken and the results observed, as this can help in future fixing initiatives.
Repair service vs. Substitute Choices
When faced with equipment malfunctions, deciding whether to change a product packaging or repair device can be a complex address and crucial choice. This choice rests on a number of essential elements, including the age of the equipment, the level of the damages, and the forecasted influence on functional effectiveness.
First of all, take into consideration the maker's age. Older machines might require even more frequent repair services, leading to higher advancing costs that can exceed the investment in a new device.
Operational downtime is an additional important factor to consider. If repairing the equipment will trigger long term delays, spending in a new device that supplies enhanced performance and reliability could be extra prudent. Furthermore, consider the accessibility of components; if substitute components are hard to find by, it might be extra strategic to replace the device completely.
Ultimately, carrying out a cost-benefit analysis that includes both instant and long-lasting effects will certainly assist in making an educated choice that straightens with your functional objectives and monetary restrictions. (packaging machine repair)
Safety Nets for Durability
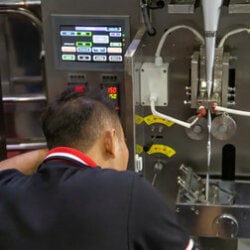
Trick safety nets consist of regular lubrication of relocating components, alignment checks, and calibration of controls and sensors. Developing a cleansing timetable to eliminate particles and impurities from equipment can significantly decrease deterioration (packaging machine repair). Additionally, keeping an eye on functional criteria such as temperature level and resonance can aid detect irregularities at an early stage
Training personnel to acknowledge indications of wear or malfunction is one more important element of precautionary maintenance. Equipping operators with the understanding to carry out basic troubleshooting can result in quicker resolutions and reduce operational interruptions.
Documentation of upkeep tasks, consisting of solution records and evaluation findings, fosters liability and promotes educated decision-making relating to repair services and replacements. By focusing on preventative procedures, companies can ensure their product packaging makers operate at peak performance, inevitably causing enhanced productivity and reduced functional expenses.
Conclusion
In conclusion, the efficient upkeep and fixing of packaging makers are extremely important for sustaining operational performance. By implementing preventive procedures, organizations can enhance device durability and make certain uninterrupted efficiency in product packaging procedures.
Recognizing the intricacies of packaging device repair service is critical for maintaining optimal performance and reducing interruptions.Routine upkeep of product packaging makers is critical for ensuring optimal performance and longevity.Packaging machines, like any complex machinery, can encounter a variety of common Look At This issues that may prevent their efficiency and performance. If fixing the maker will certainly trigger extended delays, investing in a new machine that supplies boosted performance and integrity may be much more prudent.In conclusion, the reliable upkeep and repair service of packaging devices are paramount for maintaining functional effectiveness.